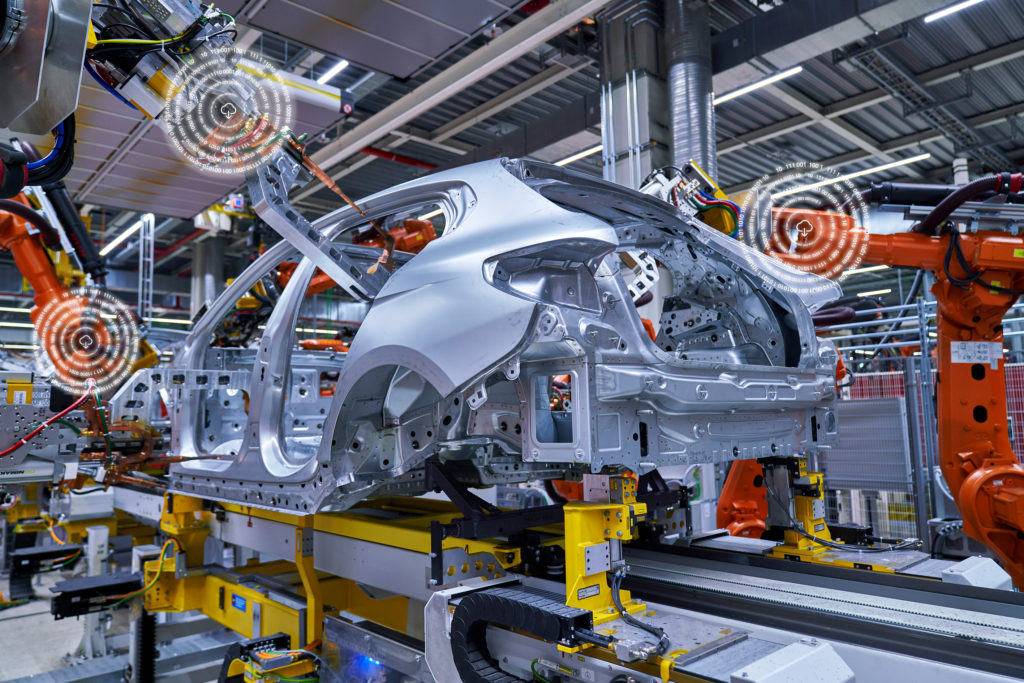
Wenn die Maschine schon vor einem Ausfall weiß, dass sie repariert werden muss.
+++ Predictive Maintenance setzt neue Effizienz-Maßstäbe durch nachhaltige Wartung bei der BMW Group.
+++ Smarte digitale Überwachung und Instandhaltung vermeidet Produktionsausfälle.
+++ Integration der Cloud basierten Plattform im weltweiten Produktionsnetzwerk der BMW Group
Die BMW Group setzt bei der Instandhaltung ihrer Produktionssysteme auf den Einsatz von Sensorik, Data Analytics und Künstliche Intelligenz. Damit wird ein zeit- oder regelbasierter Ansatz durch eine zustandsorientierte, vorausschauende Instandhaltung abgelöst: Neben der Vermeidung von teuren Produktionsstillständen, leistet die optimale Verfügbarkeit der Produktionsanlagen einen wichtigen Beitrag zur Nachhaltigkeit und Ressourceneffizienz. Innovative Predictive Maintenance Lösungen werden aktuell weltweit auf Basis einer Cloud-Plattform in das Produktionsnetzwerk ausgerollt.
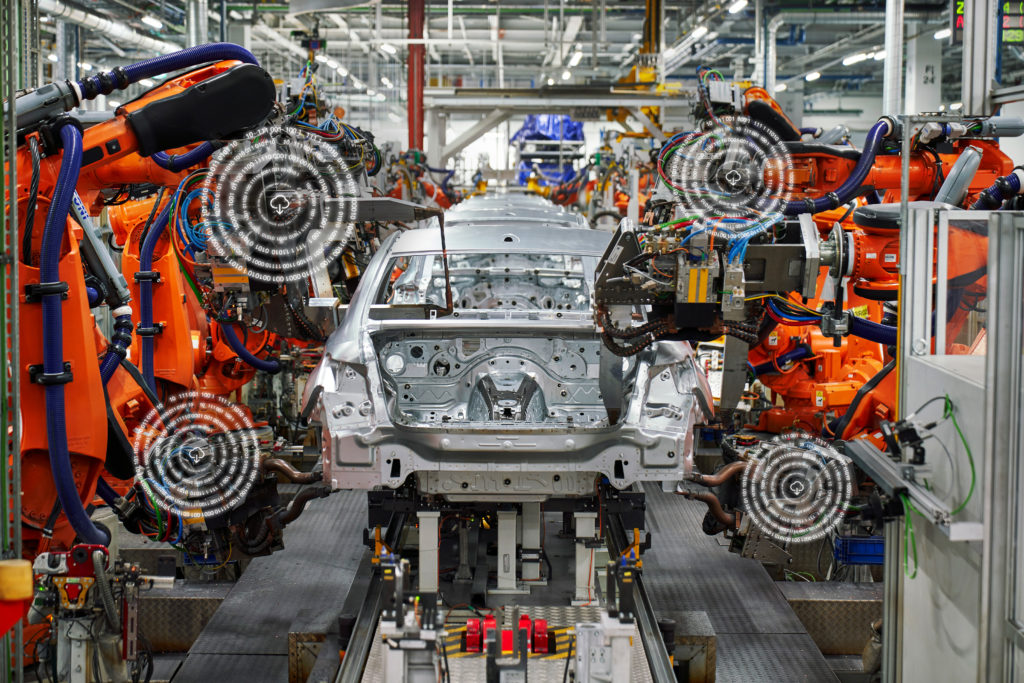
Predictive Maintenance als Frühwarnsystem der Produktion.
Ein wichtiges Thema im Zuge der Digitalisierung der Instandhaltung ist „Predictive Maintenance“: Durch das Monitoring von Maschinen- und Zustandsdaten kann vorhergesagt werden, wann eine Anlage ausfallen wird, bevor es tatsächlich dazu kommt. Der datenbasierte Ansatz hilft dabei, das Instandhaltungsoptimum zu erreichen. So können Komponenten vorsorglich getauscht und Produktionsausfälle verhindert werden. Gleichzeitig werden intakte Komponenten nicht unnötig frühzeitig ausgetauscht und damit die Effizienz und Nachhaltigkeit erhöht.
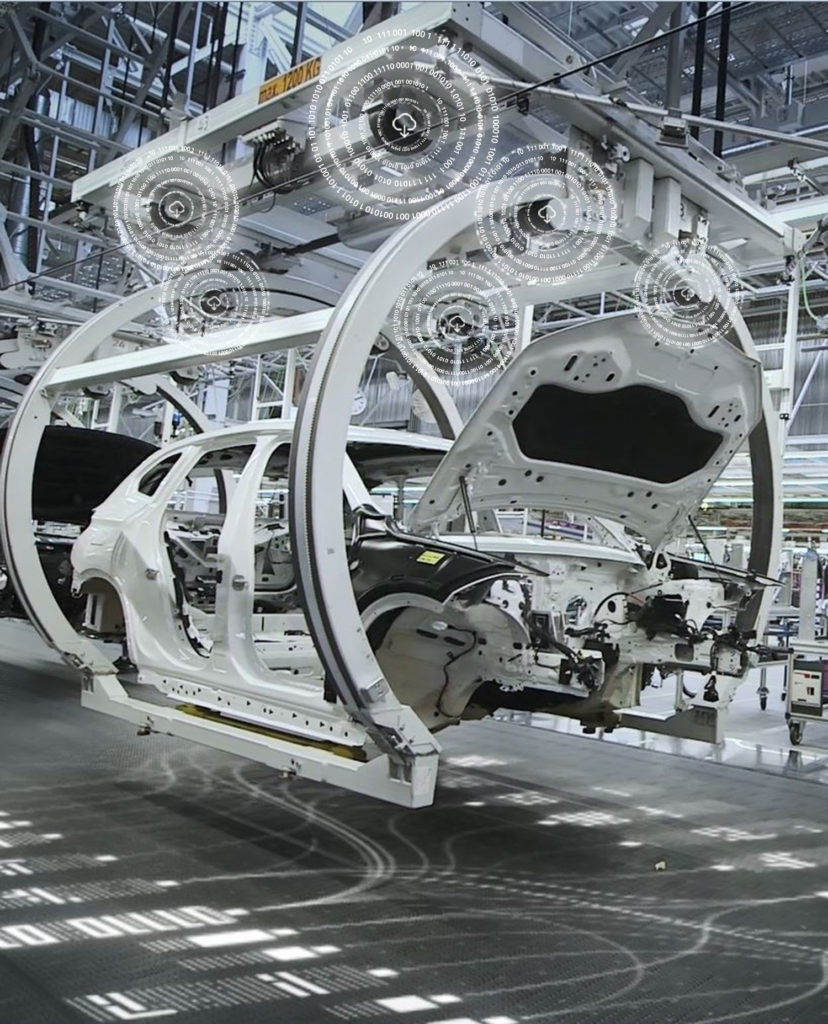
Zustandsprognose auf Basis einer cloudbasierten Plattform.
Um frühzeitig Warnungen über mögliche Produktionsausfälle zu erhalten, greift Predictive Maintenance auf eine moderne Cloud-Plattform zurück. Die zu überwachenden Produktionsanlagen werden einmalig über ein Gateway an die Cloud angeschlossen und übermitteln regelmäßig Daten – meist einmal in der Sekunde. Innerhalb der Plattform lassen sich einzelne Software-Bausteine flexibel und bedarfsgerecht zu- und abschalten, womit Anpassungen an veränderte Anforderungen in kürzester Zeit vorgenommen werden können. Durch den hohen Standardisierungsgrad der einzelnen Komponenten entsteht ein global verfügbares und hoch skalierbares System, in dem neue Anwendungsfälle einfach umgesetzt und bestehende Lösungen schnell ausgerollt werden können.
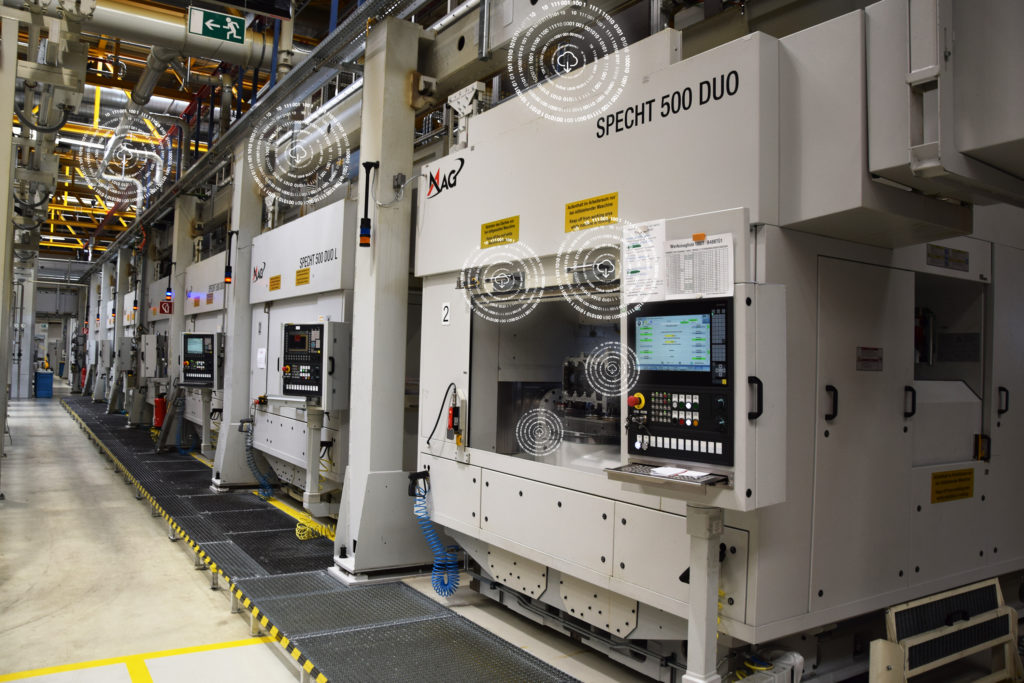
Durch Predictive Maintenance können Wartungs- und Instandhaltungsprozesse an den realen Zustand angepasst werden. Somit werden Instandhaltungsmaßnahmen nicht nur von der laufenden Produktion entkoppelt und in die produktionsfreie Zeit terminiert, sondern auch zielgerichteter, kosteneffizienter und ressourcenschonender durchgeführt. Auch eine Verlängerung von Laufzeiten erhöht maßgeblich die Nachhaltigkeit der eingesetzten Produktionsmittel. Die Bereitstellung der Lösungen erfolgt nach dem Motto: Einmal entwickelt, mehrfach in das Produktionssystem der BMW Group ausgerollt.
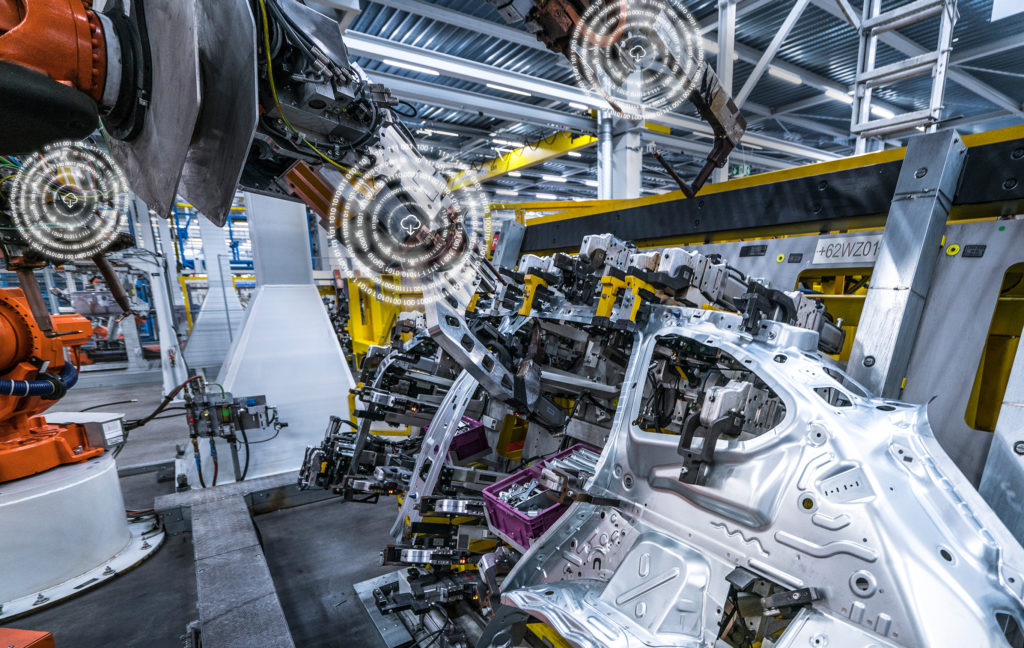
Vielfältige Einsatzmöglichkeiten.
In der Antriebsfertigung der BMW Group werden neben konventionellen Motoren auch Gehäuse für Elektromotoren in flexiblen, hochautomatisierten Anlagen mechanisch im Minutentakt gefertigt. Das hierfür entwickelte System zur vorausschauenden Instandhaltung erkennt Auffälligkeiten durch einfache statistische Modelle, sowie in komplexeren Fällen über prädiktive KI-Algorithmen. Mit Hilfe von Visualisierungen und Alarmen wird der Produktionsmitarbeiter über anstehende Wartungsarbeiten im Voraus informiert.
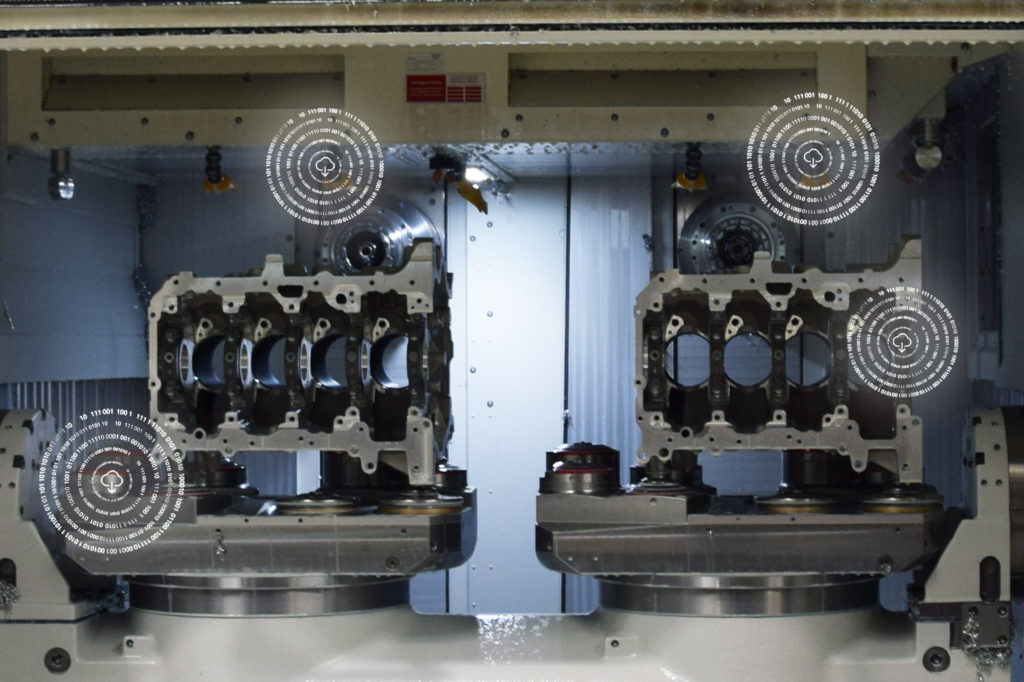
Im Karosseriebau leistet eine Schweißzange bis zu 15.000 Schweißpunkte pro Tag. Um mögliche Ausfälle während der Produktion im Vorfeld zu erkennen, sammelt eine speziell entwickelte Software weltweit die Daten der Schweißzangen und gibt diese an die Cloud weiter. Dort werden sie mit Hilfe von Algorithmen aufbereitet und analysiert. Dashboards stehen zur Visualisierung aller Daten weltweit zur Verfügung und unterstützen bei den Instandhaltungsprozessen.
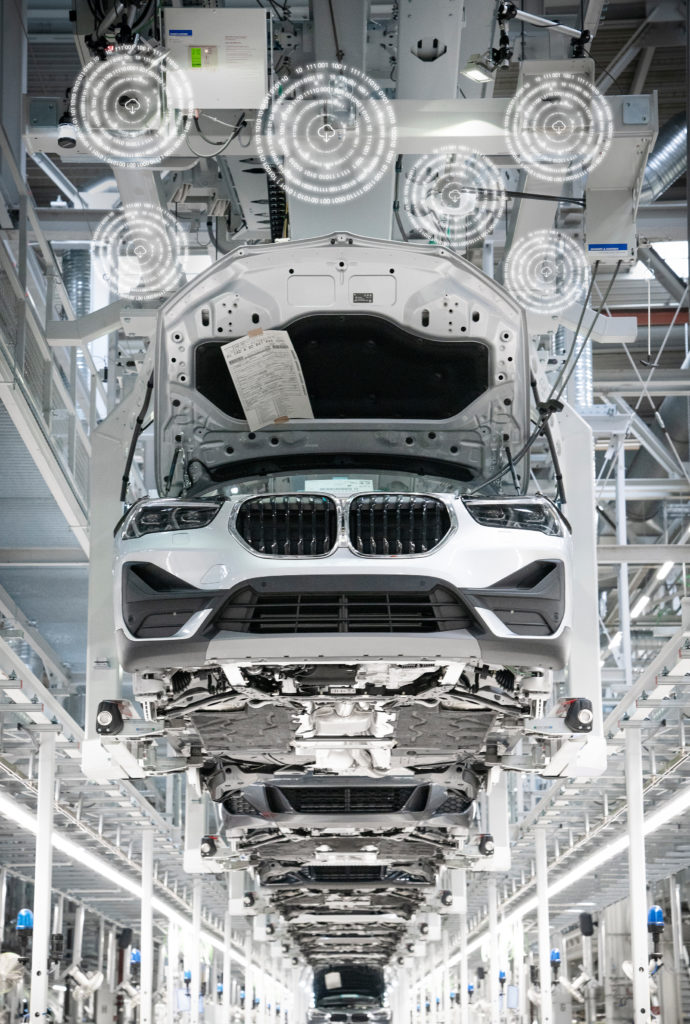
Auch in der Fahrzeugmontage beugt die vorausschauende Instandhaltung einen Ausfall von Förderelementen vor. Im BMW Group Werk Regensburg beispielsweise senden die Steuerungen der Fördertechnik Daten u.a. zu elektrischen Strömen, Temperaturen und Positionen rund um die Uhr in die Cloud-Plattform, in der sie kontinuierlich ausgewertet werden. So wissen die Datenspezialisten von jedem Förderelement zu jeder Zeit, wo es ist, wie der Zustand ist und was es macht. Auf dieser Datenbasis werden prädiktive KI-Modelle angewendet, welche Anomalien detektieren und somit Hinweise auf technische Probleme geben.
Fotos © BMW Group